- 17min
- 13377
- an opinion
No one can imagine the world without electric tools and equipment which all work with electric motors. In many electricity-powered devices, there is an electrical motor that works silently and develops the functions. But what are they? What do they do? What are their features? If these are your questions too, follow the article. To get into the issue, I start with a brief history of it.
The Evolution of Electric Motors
Michael Faraday, a British physicist, is regarded as one of the most significant of the numerous 19th-century scientists who contributed to the discovery and development of electric motors. Faraday achieved the successful rotation of a wire using a magnet and a magnetic field created by an electric current in 1821. In 1831, he developed the law of magnetic induction, paving the way for considerable advancements in electrical motors and generators.
📌 Many additional forms of electric motors, as well as architectures that might be called the classic DC motor, have been developed over time.
Following that, the practical electric motor was found rather than invented in 1872, when one of the generators on display at the Vienna World’s Fair began rotating on its own after being unintentionally linked to another generator. This led to the realization that the same principles applied to generators could also be applied to motors. Generators became a mainstay of many sectors in the twentieth century as a result of the fast rise in their practical application.
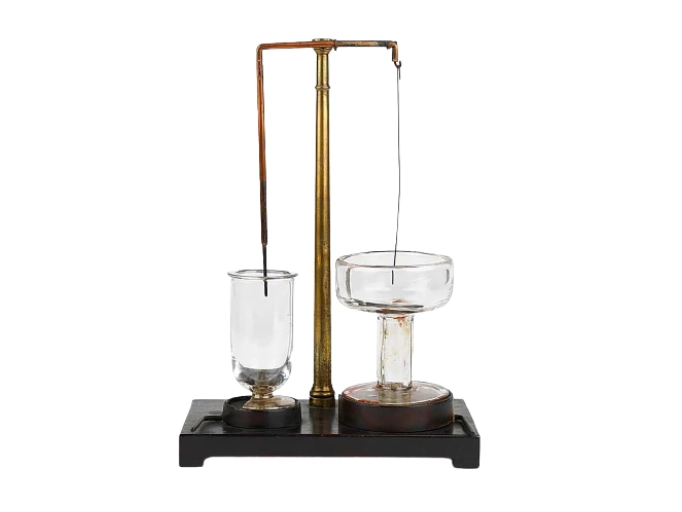
What Is an Electric Motor? What do electric motors do?
The electro-mechanical mechanism that transforms electrical energy into mechanical energy is known as an electric motor. Motors, in other terms, are devices that produce rotating force. The interplay of magnetic and electric fields is crucial to the operation of an electric motor, especially in cordless devices like cordless drills.
they generate rotational mechanical force in the armature—located on the rotor or stator—around the shaft by using electrical current to produce rotating magnetic fields. To turn electric energy into intense bursts of force and produce dynamic degrees of speed or power, numerous motor designs employ the same basic premise.
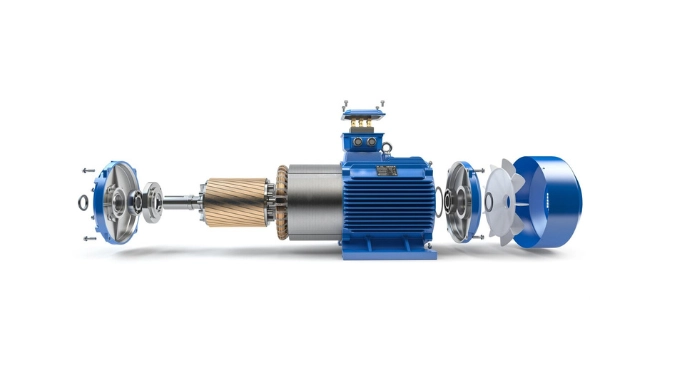
Generators and Motors
There are other energy sources such as Generators, their functions can be mistaken with that of electrical motors. Here I will debunk the misconception with a simple compare:
Generators turn mechanical energy back into electrical energy
Whereas, Electric motors convert electrical energy into rotation and various kinds of mechanical energy.
However, despite their opposing tasks, motors and generators have a lot in common in terms of design and functioning. In truth, all it takes is a simple experiment with two model motors coupled together to show that an electric motor may also function as a generator. But the two sorts of machines have traditionally been designed independently due to the distinct manner in which they are employed.
Now, let’s take a closer look at electric motors and talk about its parts and types.
Parts of Electric Motor
While electric motors vary in form and kind, many of them comprise the following parts and assemblies (starting at the center and working outward):
- Windings
- Central motor shaft
- Ball and roller bearings (to reduce friction and wear)
- Brushes (in DC motors)
- Terminals (placed on the rotor, the revolving part, or the stator, the stationary component)
- Industrial Applications of Electric Motors
- Frame and end shields
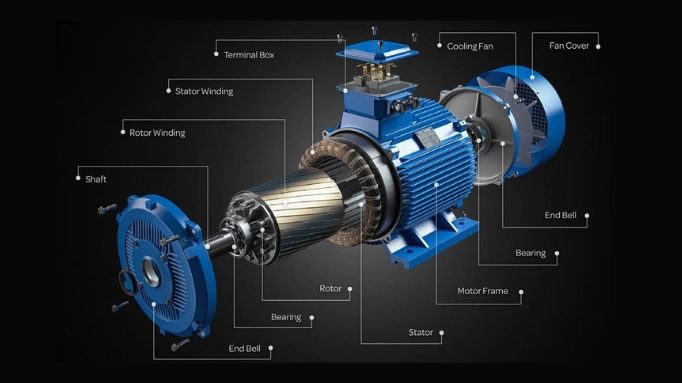
What Are the Advantages of Electric Motors?
they offer several advantages over other types of motors, including:
- High efficiency: they are highly efficient, converting a high percentage of electrical energy into mechanical energy. This means that they can operate with less wasted energy compared to air motors, resulting in lower operating costs and reduced environmental impact.
- Low maintenance: Electrical motors have fewer moving parts compared to other types of motors, which means they require less maintenance and have a longer lifespan.
- Instant torque: They can provide instant and consistent torque, which is especially important in applications where acceleration or deceleration is required.
- Quiet operation: Electric motors operate quietly and do not produce exhaust fumes or emissions, making them ideal for use in indoor or enclosed spaces.
- Variable speed control: They can be easily controlled to provide variable speeds, allowing for greater precision and flexibility in many applications.
- Easy integration: Electric motors can be easily integrated with electronic control systems, making them ideal for use in automated and robotic systems.
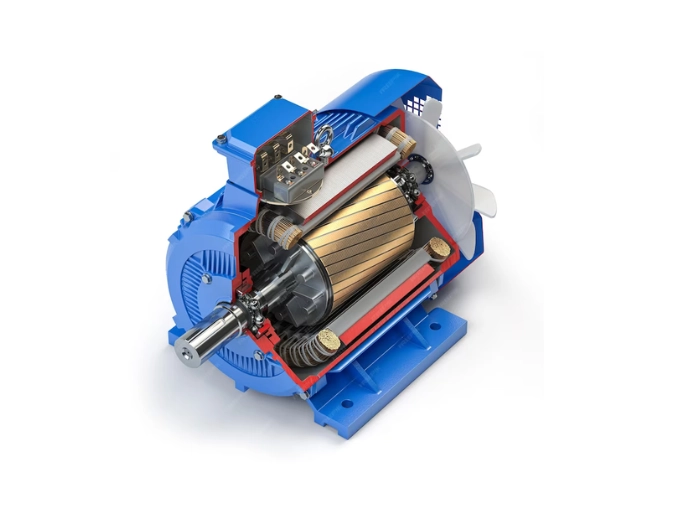
Related Article : All About The Dual-Speed Motors
What Tools Use Electric Motors?
Electric motors can be found in a wide variety of tools, both handheld and stationary. Here are some examples of tools that commonly use electric motors:
- Power drills and drivers
- Sanders and grinders
- Circular saws and table saws
- Jigsaws and reciprocating saws
- Planers and jointers
- Air compressors
- Lawn mowers and trimmers
- Leaf blowers and vacuums
- Pressure washers
- Sewing machines
- Food processors and blenders
- Vacuum cleaners
- Fans and air purifiers
- Exercise equipment, such as treadmills and stationary bikes
- Electric vehicles, such as cars, bikes, and scooters
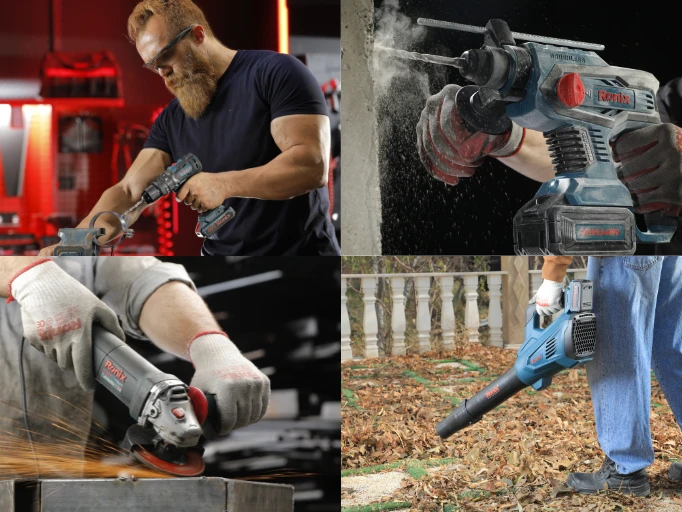
Different Types of Electric Motors
When it comes to different types of electric motors, I should mention that they come in a variety of designs with different operating and safety characteristics, but some of the main electric motor types are the following:
- Alternating Current (AC)
- Direct Current (DC)
How Does an AC Motor Work?
An AC motor is a mechanism that transforms AC electrical power into mechanical power. This type of electric motor includes three types:
- Induction motors
- synchronous motors
- linear motors
AC electrical motors are the most often used in the business because they offer various benefits:
- They are simple to construct
- They are more economical due to lower start-up consumption
- They are sturdier and therefore generally have a longer lifespan
- They require little maintenance
- They are simple to construct
How Does an DC Motor Work?
A DC motor is a mechanism that transforms DC electrical power into mechanical power. Its operation is based on the basic idea that when a current-carrying conductor is put in a magnetic field, a force is applied to it, and torque is generated.
DC motors are also highly prevalent in industrial settings because, depending on the format they offer considerable advantages:
- They are precise and rapid
- Their speed can be regulated by altering the supply voltage
- They are simple to install, even in mobile (battery-powered) systems
- The starting torque is great
- They start, stop, accelerate, and reverse swiftly
What Is the Difference Between AC and DC Motors?
Each motor type has its own set of qualities that make it ideal for a variety of commercial and industrial applications. AC motors, for example, are versatile and simple to use. The following are some of their additional features:
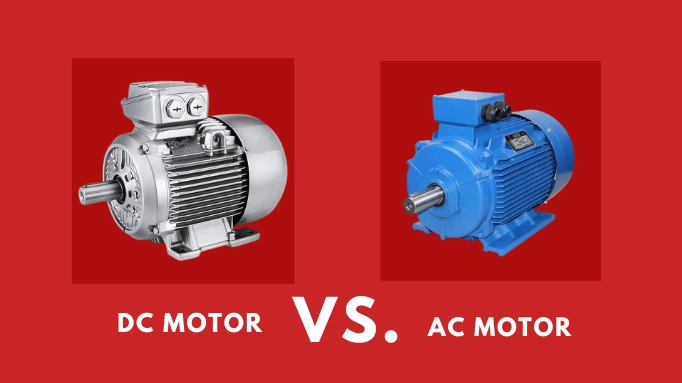
- Low beginning power requirements that safeguard receiving end components
- Controllable beginning current levels and acceleration
- VFD or VSD add-ons that can adjust speed and torque at various phases of use
- Longer durability and life spans
- Multi-phase setup capabilities
DC motors have their own set of traits, including:
- easy installation and maintenance
- High beginning power and torque
- Quick start-up, stop-up, and acceleration reaction times
- Available in a variety of standard voltages
Comparing these two, an important question arises:
Which is more powerful, an AC or a DC motor?
AC electric motors are typically thought to be more powerful than DC motors because they can create more torque with a higher current. DC motors, on the other hand, are more efficient and make greater use of their input energy. AC and DC motors are available in a variety of sizes and strengths to satisfy the power requirements of any business.
After comparing AC and DC electric motors and getting enough data about them, let’s get deeper in DC motors and check two types of DC electric motors them that play a leading role as power tool motors:
Brushless Vs. Brushed DC Motors
Brushed and brushless motors are the two most prevalent types of DC electrical motors (or BLDC motors).
A brushed or brushless DC motor may be utilized in numerous applications. They work on the same principles as coils and permanent magnets in terms of attraction and repulsion. Both offer benefits and drawbacks that may lead you to prefer one over the other, depending on the needs of your application. Here are their features:
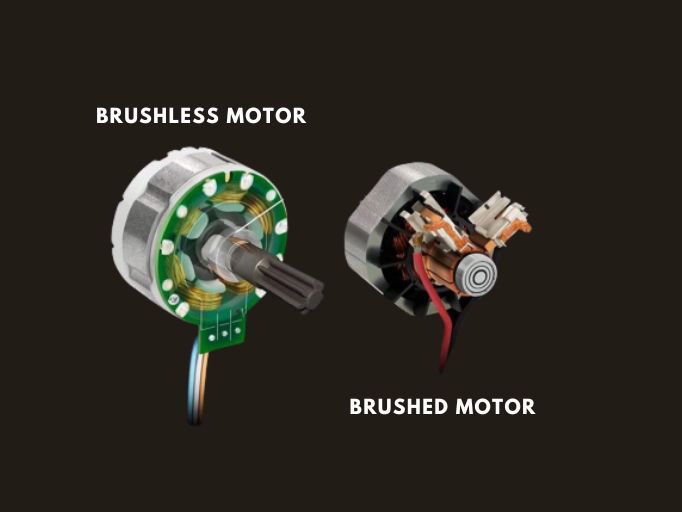
Brushed Electric Motor
DC brushed motors, as their names suggest, feature brushes that are utilized to commutate the motor and cause it spin. They have their specific structure including the following parts:
- Stator—a permanent magnet-encased enclosure.
- Armature is a rotor with a number of electromagnets installed on it. Inside the stator, it spins freely.
- Commutator— A metal ring attached to the armature shaft is known as a commutator.
- Brushes— To maintain electricity flowing to the armature coils, carbon slabs remain in contact with the commutator.
Brushless Electric Motor
In Brushless electric motors, brushes are removed, so electronic control replaces the mechanical commutation function.
Brushless electrical motors today overcome many of the drawbacks of brushed motors by combining higher output power, smaller size and weight, improved heat dissipation and efficiency, wider operating speed ranges, and extremely low electrical noise. Brushless motors feature no electrical connections that might wear out, resulting in greater dependability and shorter maintenance intervals in commercial and industrial applications.
Both AC and DC motors can be designed to operate at constant speed or dual speed. The choice of which motor to use will depend on the specific application and its speed control requirements.
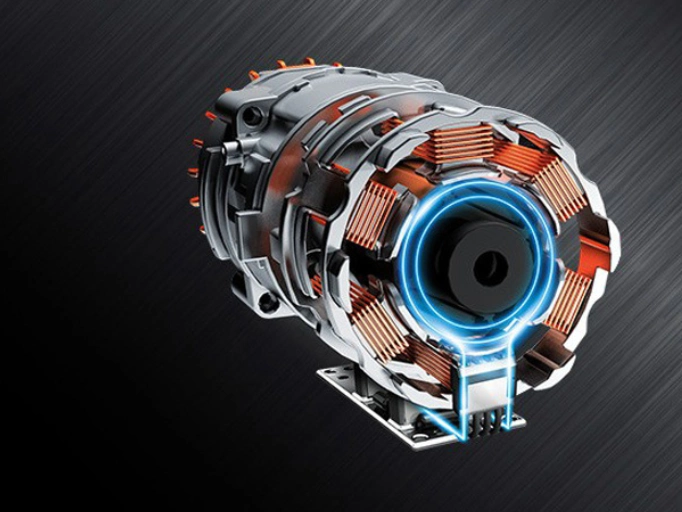
The Constant Speed Electric Motor
The process of selecting a motor and gearhead should begin with a thorough examination of the motor’s specifications to ensure that the motor you choose meets the application’s requirements. What you need to begin your selection is some factual and useful information the motors. The constant speed electric motor combines an induction motor with a power on activated type clutch and brake. It’s perfect for frequent start-and-stop operations. Suitable for situations where the motor is run at synchronous speed independent of load torque and the motor is started, stopped, and reversed frequently.
The Dual-Speed Motors
Dual-speed motors are a cost-effective choice for applications that only require two speeds, while also lowering the chance of failure. These motors are often constructed with an operational speed and a slower speed for easier starting. Without the need of a frequency converter, dual speed motors may push fans, pumps, hoists, and other machinery at two distinct speeds.
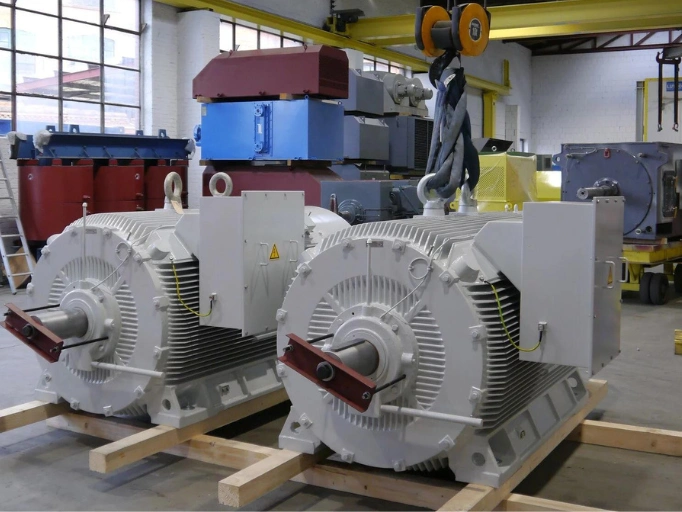
What Is the Difference Between Constant Speed and Double Speed Tools?
- One main difference is the gearbox design. Constant speed tools provide maximum speed and power, but dual speed tools can be configured for two modes: fast and slow.
- Working with a two-speed tool is more efficient. On the contrary, a tool with a constant speed provides a lot of power and is very convenient for projects that require a lot of effort.
- A double-speed tool can be used for various types of work, but a constant-speed device has been designed for a special purpose. For example, a double-speed drill is used for drilling, impact drilling and wrapping. But an ordinary drill is only suitable for drilling operations.
- The versatility of single-speed tools is much less than that of two-speed tools, even if the power is the same.
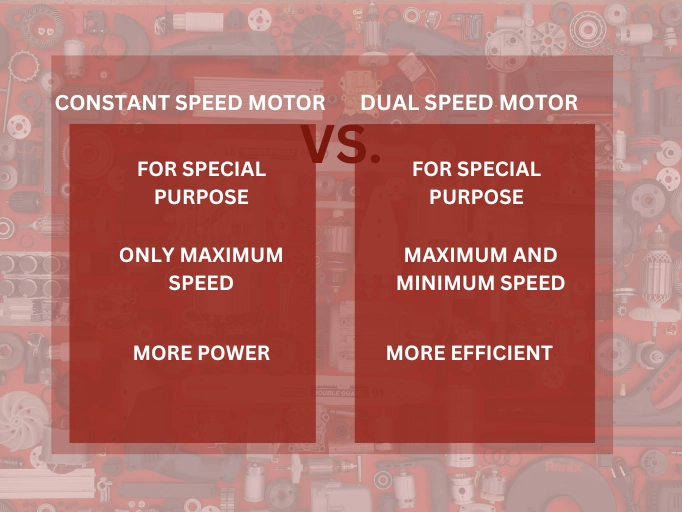
After a long journey in the world of DC and AC motors, let’s take a look at some of the leading features of Electric motors: RPM and Torque.
What Is Rotational Speed (RPM)?
Motor’s rotational speed is the number of rotations of a tool per unit of time and is measured in revolutions per minute (RPM). In fact, RPM is a unit of measure used to show the no-load speed or frequency of a power tool.
The turning speed is considered an important factor depending on the type of work that we are going to carry out. Therefore, when we use an electric machine to work on hard surfaces such as concrete, we are interested in opting for more revolutions per minute.
This speed also has a direct relationship with the type of tool we use. For example, cordless drills typically offer a maximum speed of around 2000 RPM, while most corded drills typically operate at a speed of 3000 RPM.
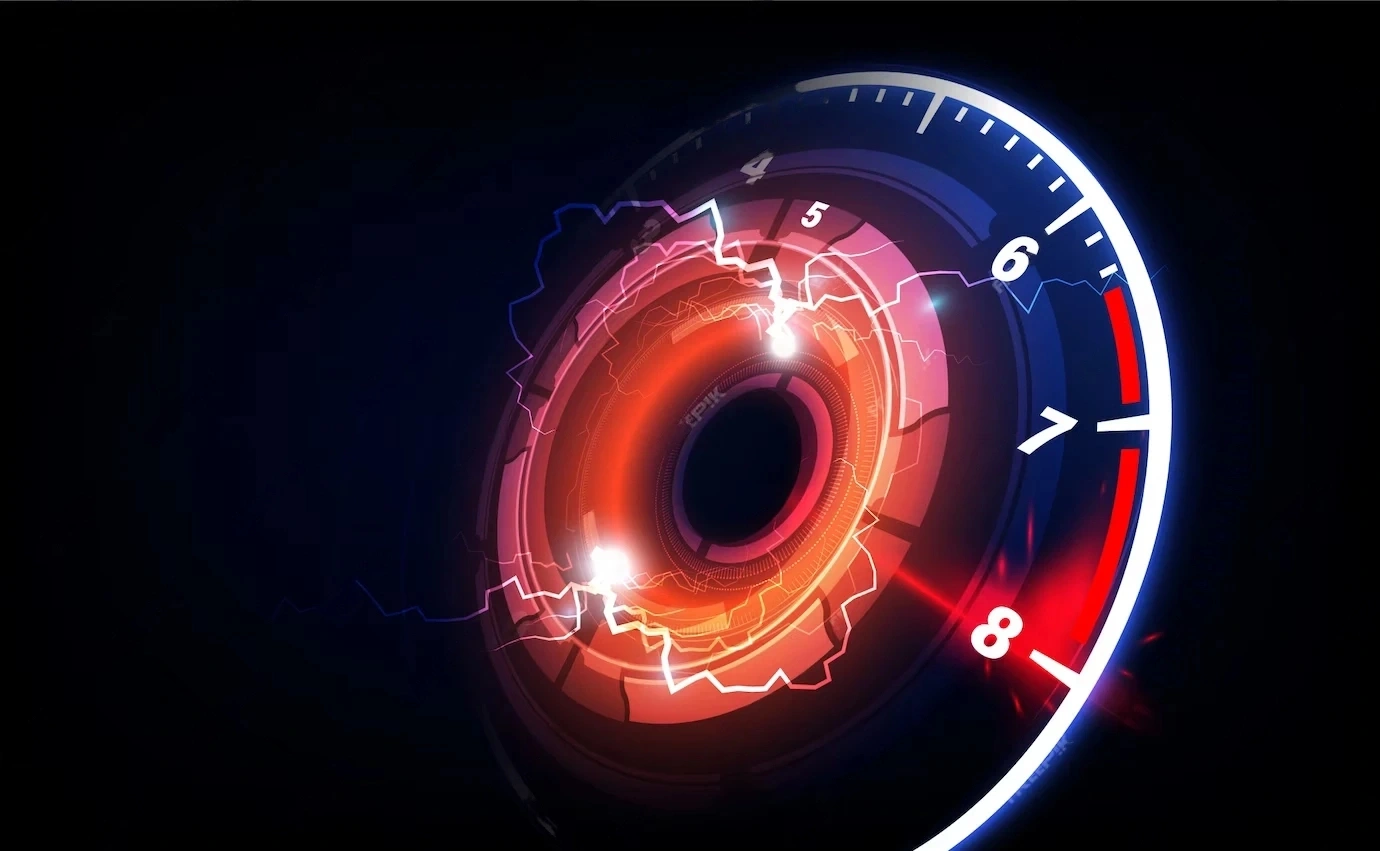
What Is an Electric Motor’s Torque?
The force that causes an item to rotate, measured in Newton Meters (Nm), is the greatest indicator of how strong your drill or impact driver is. The greater the figure in newton meters, the more twisting force it will give.
To measure the torque of an electrical motor, there are two methods:
Traditional Torque Rating Measurement Method:
- Drilling into the rig
2. Securing the chuck to a stationary spindle
3. Drill is completely operational.
4. Drill torque is measured at 0 revolutions per minute (does not measure speed)
New Power Rating Measurement Method:
- Drilling into the rig
2. Securing a chuck to a spinning spindle
3. Drill is completely operational.
4. Torque loads are becoming more prevalent.
5. Multiple data points are used to calculate drill speed and torque.
Power Tool Torque Settings
When driving screws into tougher materials, you’ll need to go slower and apply more torque. You can adjust the depth of your drilling without inflicting any harm if you get these parameters perfect. To achieve the greatest results while drilling holes, the tougher the material, the faster the speed.
What Is the Difference in Turning Speed and Torque?
The concept of tightening torque expresses the amount of rotating force produced by the motor of a power tool. As an example:
- The rotary force of a screwdriver is used to tighten screws, nuts, or anything similar.
- Torque, which is measured in terms of Newton meters (Nm), is the force dedicated to turning an object and is the best indicator to find out the practical power of a power tool.
However, the rotational speed, as the name describes well, shows the rotational speed of an electric motor. For example, the higher the RPM of a drill, the higher the speed of the bit.
Important note: Torque and rotational speed are not only different things, but they also have a completely inverse relationship. In simple terms, when a power tool offers high torque, it will have a low turning speed, and vice versa.
Conclusion
Considerations such as power source type, internal construction, application, and kind of motion output can all be used to classify electric motors. Aside from AC vs DC, motors can be brushed or brushless, single-phase, two-phase, or three-phase, and air-cooled or liquid-cooled.
Vacuum cleaners, dishwashers, computer printers, fax machines, video cassette recorders, machine tools, printing presses, autos, subway systems, sewage treatment facilities, and water pumping stations are all examples of electric motors’ importance in modern life. The new period, on the other hand, heralds a greater focus on detail as a result of development, law, and the need to remain competitive. As a result, systems become more complicated, and resources scale up in response. Making an expert system is unquestionably an engineering problem, and minor percentage efficiency increases can help pave the path to the optimized/green future we seek. The objective is to fine-tune and develop motor designs and control algorithms.
FAQ âť“
What are Electric Motors Used For?
Electric motors are used for converting electric energy into mechanical energy.
What Are Different Types of Electric Motors?
Electric motors are offered in two main types: Alternating Current (AC), Direct Current (DC). While AC motors have three types: Induction motors, synchronous motors, linear motors.
What Tools Use Electric Motors?
Electric motors can be found in a wide variety of tools, both handheld and stationary. Here are some examples of tools that commonly use electric motors: Power drills and drivers, electric saws, air compressors, exercise equipment, electric vehicles, such as cars, bikes, and scooters.
What Is the Function of Motor in a Tool?
Electric motors are in charge of converting electric energy into mechanical energy.
Do Power Tools Use Ac or Dc Motors?
Both AC and DC motors have their advantages and disadvantages, and the choice of motor will depend on factors such as power requirements, efficiency, weight, and cost.
When compared to brushed DC motors, what are the benefits of brushless DC motors (BLDC motors)?
Brushless DC motors (BLDC motors), which do away with brushes and commutators with mechanical contacts, are low-noise, low-maintenance, and capable of high-speed operation.
What is the brush material in a DC motor?
Metal, carbon, and metal-carbon composites are common materials for brushes. Some metal brushes use a commutator to apply precious metals like gold to a contact surface. A brush’s substance is carefully selected based on electric voltage/current as well as economic considerations.
What are the components of a basic motor?
An armature or rotor, a commutator, brushes, an axle, a field magnet, and some type of DC power source make up a basic motor.
What is the maximum lifespan of an electric motor?
If operated under typical operating circumstances, an electric motor can last between 15 and 20 years under test settings.
Is it better to use a DC or an AC electric motor?
Although AC motors are more powerful and require less maintenance, DC motors are more energy efficient. The use of the electric motor has an impact on whether AC or DC is chosen.

Amanda Smith
6 December 2021
Thank you for this informative article on Electric Motors